
While the strut diameter was fixed to 6 mm, the lengths of the strut were 10, 20, 30, 40, and 50 mm. The vertical printing method was selected for the following printed structures. The relative density of the Three crushing modes The geometrical parameters are assumed as t = 15 mm, ω = 60°, d = 6 mm, and l is a variable. The parameters t, d, l, and ω represent the distance between two struts, strut diameter, strut length, and inclination angle, respectively. The schematic diagram of the utilized pyramidal lattice structure is shown in Fig. The design was modified based on both strut diameter and length. Then, the compression performance and energy absorption characteristic of the lattice structures with the same strut diameter but different strut lengths were studied.Ī pyramidal lattice structure was designed to study its compression properties. The method to print the structure was first studied. In this paper, polylactic acid (PLA) was selected as three-dimensional (3D) printing material. designed an hourglass lattice structure, and presented an analysis of its in-plane and out-of-plane compression performances. An octet truss lattice structure was designed via selective laser melting, and its specific energy absorption was high. Micro-lattice structures were manufactured via selective laser melting, and its compression property was studied. studied the compression and shear properties of pyramid structures under vacuum thermal cycling. tested sandwich panels with hollow Al-Si tube core, and reported that the structure achieved superior specific strength. used a combination of numerical simulation and experiment to study the impact performance of the pyramidal structure, and the result shows that the impact location would greatly influence the impact damage. Results show that bio-based 2-D lattice structure has a superior behavior compared to other biomaterials. ,, designed and optimized the compressive behavior of bio-based 2-D lattice structure. The prepared composite pyramid lattice sandwich structures have excellent mechanical properties. ,, ,, , presented a fundamental study on the mechanical behavior of composite sandwich structures with pyramidal truss core. The mechanical property and energy absorption of lattice structures prepared by different methods were studied. Lattice truss and anisogrid structures have excellent specific stiffness, specific strength, and have been applied in transportation structures for their lightweight, ,, , and protective structures for their excellent energy absorbing ability. Appropriate printing method and relative density could make the 3D printed pyramidal structures achieve excellent specific energy absorption. Theoretic analysis and finite element method (FEM) were performed to investigate the compression behaviors of the vertically printed lattice truss materials. Three post failure styles of the vertically printed lattice truss structures were observed, including strain-hardening, stable deforming and softening and depending on the slenderness ratio of the strut. However, the vertically printed lattice truss structures had excellent ductility and their struts never broken off during compression. These two types of printed lattice truss materials had close strength and rigidity. Quasi-static axial compression tests were conducted to study the mechanical properties and energy absorption of the pyramidal lattice truss structures.
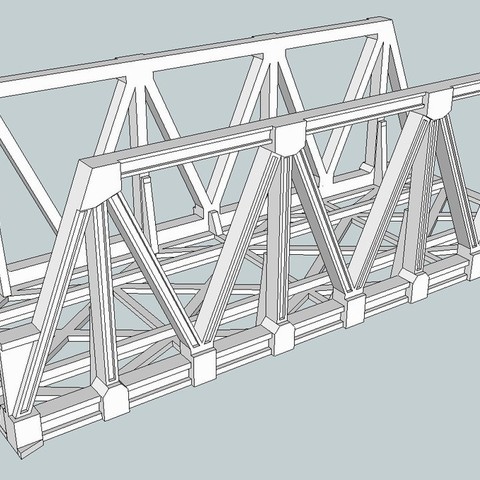
In this research, pyramid lattice truss structures were designed and manufactured by three-dimensional (3D) printing technology through horizontal printing and vertical printing manners, respectively. The lattice truss structure is a porous lightweight periodic structure with high specific stiffness and specific strength.
